All rights reserved by PRINTECH Corporation Ltd. | Powered by DIGITAL MANGO
THE RMGT 9
Providing optimum solutions for printers seeking cost savings
The new RMGT 9 – regenerated with new styling and lineup
Specifications
Model
ST (straight press)
PF (convertible perfector)
Max. printing speed
16,000 S.P.H.
13,000 S.P.H.
Max. sheet size
640 x 920 mm
Straight printing: 640 x 920 mm
Perfecting: 635 x 920 mm
Min. sheet size
290 x 410 mm
Straight printing: 290 x 410 mm
Perfecting: 370 x 410 mm
Max. printing area
615 x 900 mm
615 x 900 mm
Paper thickness
0.04 – 0.6 mm
0.04 – 0.4 mm
The new RMGT 9 of Al-size offset presses handles various print jobs
with exceptionally high performance. Joining the proven 920 model with its extensive lineup, including convertible perfectors in up to ten colors,
the 940 model is designed to accommodate an even wider range of jobs. This model is capable of running sheet sizes up to a maximum of 940 mm in width with a 930 mm wide printing image area and has successfully adopted many of the sophisticated functions found in the flagship RMGT 10. The high-speed separator, automatic nip checking function, and a host of other performance-enhancing features ensure that the RMGT 9 continues to deliver consistently high productivity.
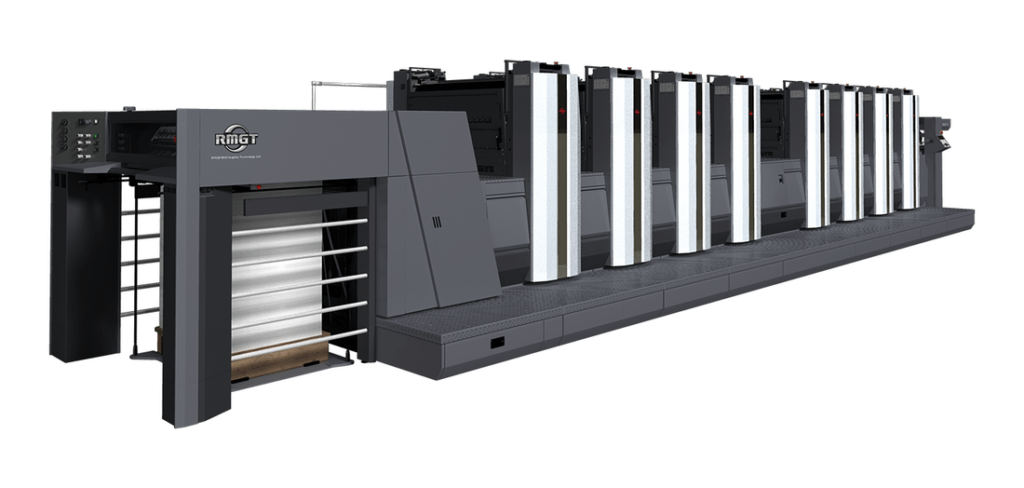
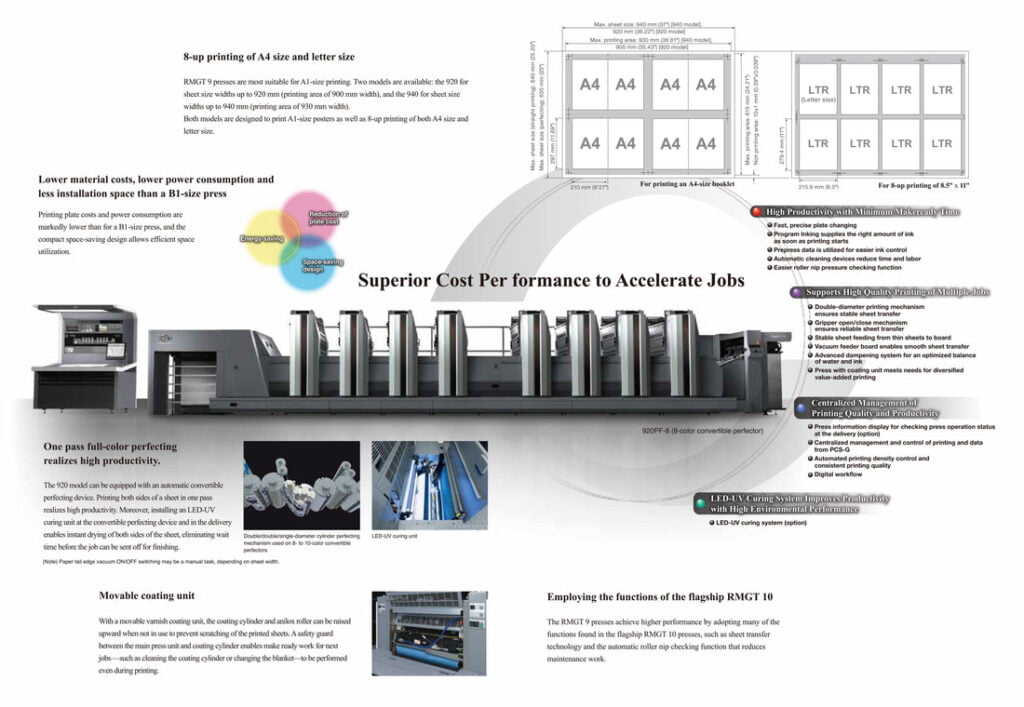
High Productivity with Minimum Makeready Time
The key to higher productivity for diverse short-run printing is shorter makeready time. With Program Inking for quick and easy color setting, an automatic plate changer and automatic cleaning devices, the majority ofmakeready work is fully automated.
Fast, precise plate changing
SPC semiautomatic plate changer comes as standard and allows plates to be changed quickly and accurately. Plate changing can be automated with the Smart-FPC * and FPC * fully automatic plate changer for even greater work efficiency.
* Option
* Option
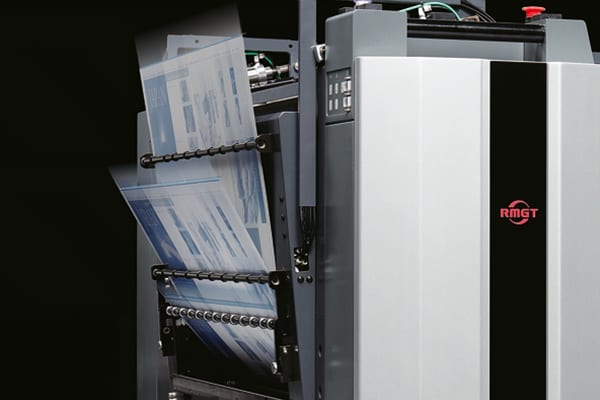
Prepress data is utilized for easier ink control
By analyzing pre-press data with PPC Server ill (or Ink Volume Setter)*, the ratio of the image area is calculated. Based on the image area data, the PCS-G printing control system automatically selects the conversion curve for each color, sets the opening of the ink fountain keys, and controls the ink rollers.
* Option
* Option
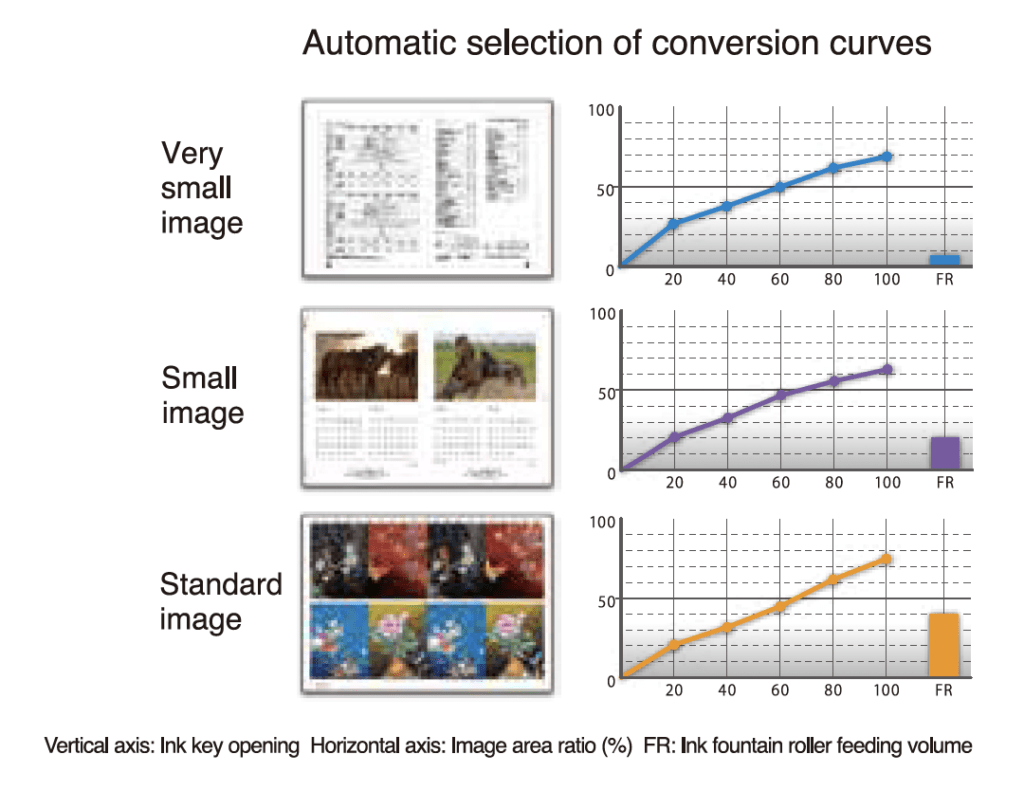
Automatic cleaning devices reduce time and labor
The automatic blanket and ink roller cleaning devices* can be centrally controlled from the PCS-G printing control system, including setting the start of cleaning for each printing unit and selecting the cleaning pattern according to the amount of cleaning required.
• Option
• Option
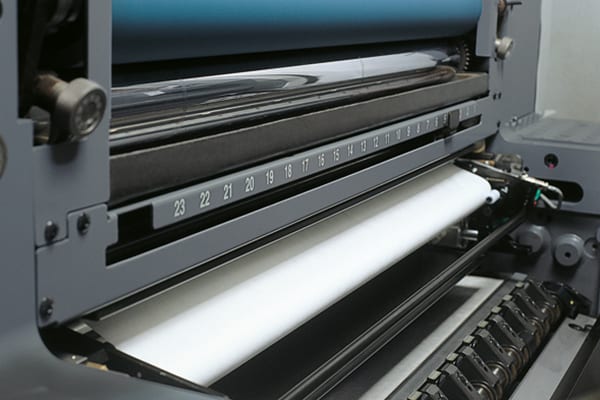
Easier roller nip pressure checking function
The one-touch nip pressure adjustment position cue function and automatic roller nip pressure checking function vastly reduce the amount of labor required during maintenance work. Nip checking is remarkably easier on the press with the nip checking mode that prints actual nip width on a single sheet pass.
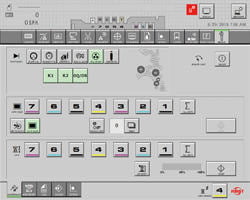
Program Inking supplies the right amount of ink as soon as printing starts
Ink is automatically supplied to match the print image. After the set number of sheets has been printed, the ink on the rollers is automatically returned to an even state to move smoothly on to the next job.
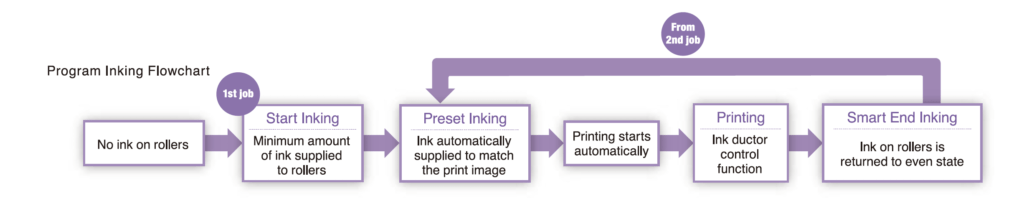
Supports High Quality Printing of Multiple Jobs
The RMGT 9 employs the same advanced air management technology found in all RMGT 10 presses to enhance sheet transfer accuracy. Stable printing quality and color reproduction are maintained by employing high precision mechanisms built with the toughness and durability that retain printing precision over long periods of time. Multiple jobs are supported by an uncompromising standard of press performance.
Double-diameter cylinders ensure stable sheet transfer
The printing unit consists of the double-diameter impression cylinder and transfer cylinder. The large radius of curvature ensures stable sheet transfer by suppressing flapping even when printing on heavy stock and film.
Gripper open/close mechanism ensures reliable sheet transfer
Each gripper shaft features a torsion bar-type gripper open/close mechanism. Reliable gripper-to-gripper sheet transfer at any operation speed ensures stable registration accuracy.
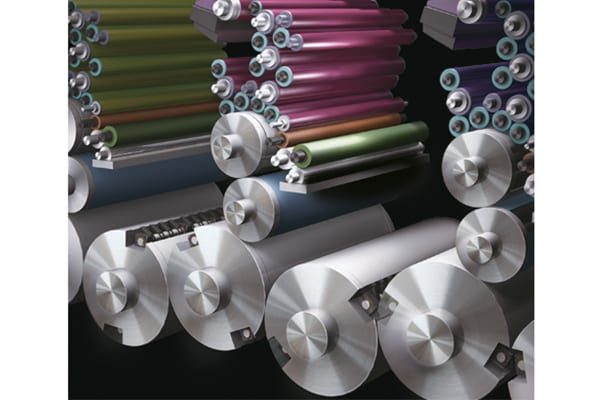
Stable sheet feeding from thin sheets to cardboard
The same high-speed, high-performance separator equipped on RMGT 10 presses is also equipped on RMGT 9 presses. From thin 0.04 mm sheets to thick 0.6 mm stock, sophisticated air management technology ensures each sheet is fed precisely even during high-speed press runs. This stock handling capability offers a wide range of applications from poster to package printing.
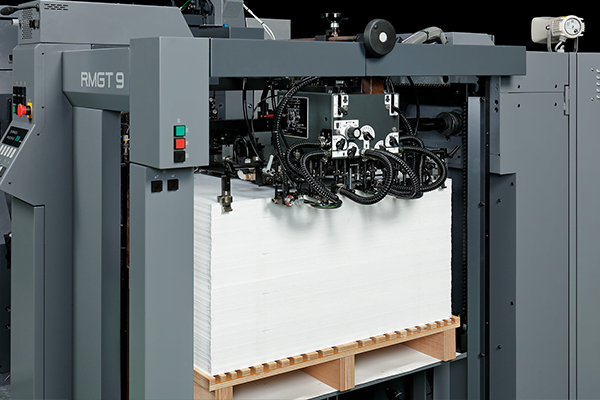
Vacuum feeder board enables smooth sheet transfer
The vacuum feeder board ensures smooth, stable sheet feed from the feeder board to the front lay. An integrated brush and runner wheel mechanism shortens the time needed to change sheet sizes. A pneumatic pull side guide* minimizes contact scratches when feeding delicate substrates.
*Option
*Option
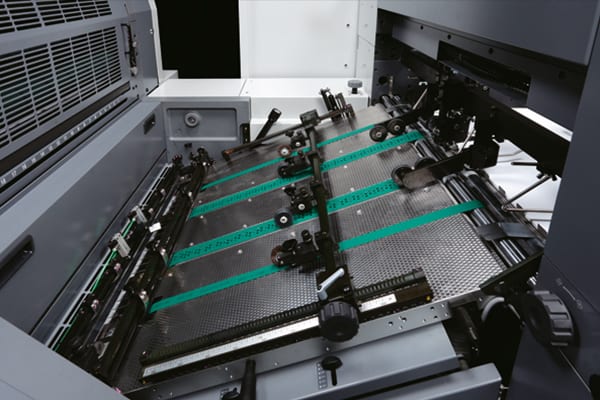
Advanced dampening system for
an optimized balance of water and ink
The R-matic continuous dampening system assures a uniform dampening supply on the plate surface to reproduce sharp dots, glossy solids and finely detailed text. This system also allows non-alcohol printing. Switching between integrated mode and separated mode from the touch-panel display is easy, in order to exactly match the image and characteristics.
The R-matic-D * Continuous Dampening System with Hickey Removing Function and R-matic-D Remote* Continuous Dampening System with Remote ON/OFF Hickey Removing Function substantially reduce hickeys on plates by adopting a drive mechanism for the water form roller that creates a rotational speed difference between the water form roller and plate cylinder.
*Option
The R-matic-D * Continuous Dampening System with Hickey Removing Function and R-matic-D Remote* Continuous Dampening System with Remote ON/OFF Hickey Removing Function substantially reduce hickeys on plates by adopting a drive mechanism for the water form roller that creates a rotational speed difference between the water form roller and plate cylinder.
*Option
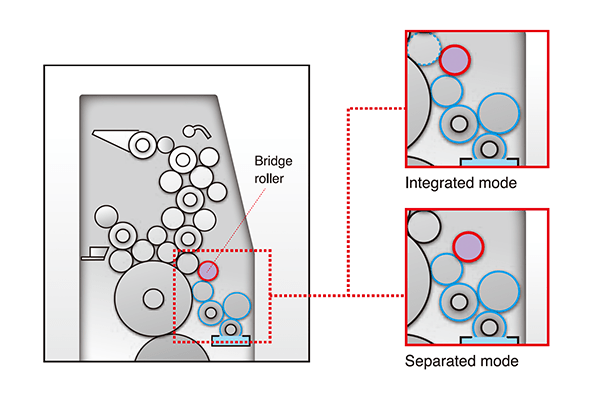
Centralized Management and Control of Printing Quality and Productivity
The RMGT 9 forms an integral part of the optimal digital work flow centered on the Printing Management System or PCS-G. With connections to an MIS designed for CIP4-JDF, a color management system linked to pre-press data, and other pre- and post-press functions, centralized management and control of printing quality and productivity is realized in the optimization of printing operations.
Press information display*
for checking press operation status at the delivery
Real-time viewing of sheet transfer by press-mounted video cameras is available on the live-view monitor at the press operation console. The information display features a monitoring function to show ink key supply volumes, image area data, job progress, print density measurement results, and operating conditions of safety devices. The screen can be viewed on a tablet connected to a Wi-Fi network, allowing remote operation at locations away from the delivery section.
The press information display contributes to a comfortable operational environment.
(Normally, three cameras are installed, but up to a maximum of ten can be accommodated.)
* Option
The press information display contributes to a comfortable operational environment.
(Normally, three cameras are installed, but up to a maximum of ten can be accommodated.)
* Option
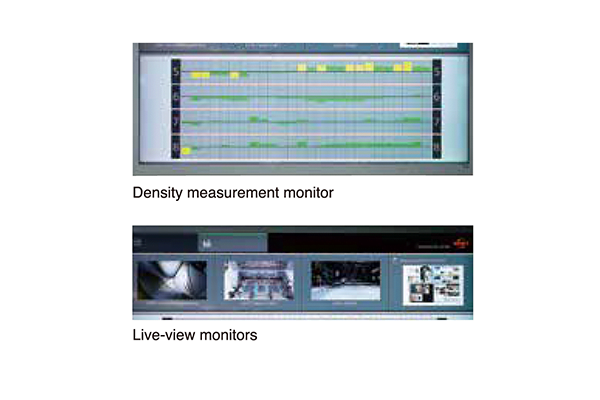
Centralized management of printing and data from PCS-G
The PCS-G printing control system acts as a printing control center, provides centralized management of entire processes from makeready to printing completion, including ink density adjustment., registration, color adjustment., water control, printing settings, cleaning and other operations. It also allows centralized management of operation and maintenance information such as maintenance history and press operation logs.
Automated printing density control and
consistent printing quality
The optional PDS-E SpectroJet* and PDS-E SpectroDrive * printing density control systems use a spectrophotometer to measure the color bar on a printed sheet and calculate the correction values as the difference between the printed sheet and OK sheet. These correction values are then fed back to the PCS-G to automatically control the opening and closing of the ink fountain keys for much faster color matching. A preset number of sheets are also sampled and measured during printing; this data is fed back to the PCS-G to minimize density fluctuations and maintain consistent printing quality from start to finish.
*option
*option
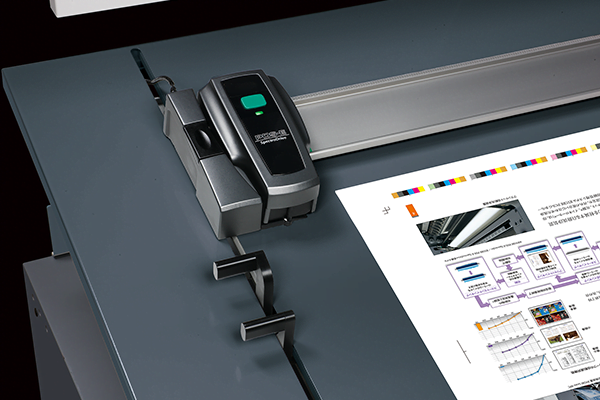
Digital Workflow
A digital workflow can be established to integrate the entire press room, prepress, and other internal sections. With the IPC and PPC servers as an interface, you can not only implement MIS, CIP4 and JDF, but also easily connect to other management systems and prepress processes you have established separately.
MIS connection software {CIP4-JDF)*
MIS connection software connects a CIP4-JDF compatible MIS (Management Information System) and PCS-G printing control system for real-time printing process management.
Print Job Manager*
The optional Print Job Manager press operation control system connects compatible presses via a network to manage the production schedule and transmit printing job data. It also collects data on press operating status in real time and automatically generates production analysis data.
PPC Server (PPC Server III)*
This server converts image area ratio data generated by CIP3/CIP4-PPF and CIP4-JDFenabled prepress systems and provides data on ink key opening volume.
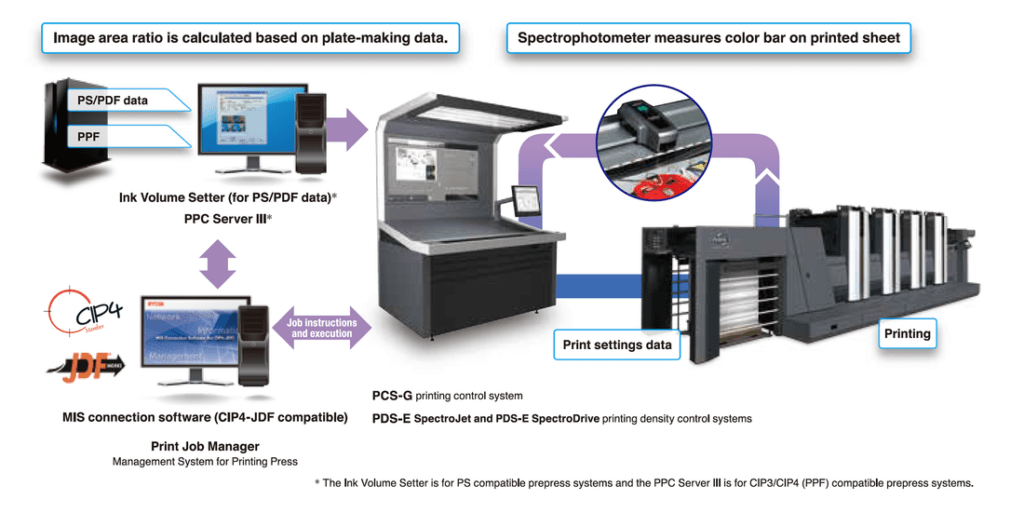
LED-UV Curing System* Improves Productivity with High Environmental Performance
RMGT is the first press manufacturer worldwide to put LED-UV curing systems into commercial production for sheet-fed offset printing. RMGT continues to lead the industry in this area by improving and developing the curing system, which features outstanding environmental performance.
*option
Features of LED-UV curing system
Low power consumption
Power consumption of the LED-UV curing system is only 10 percent* of that of conventional UV lamp system. In addition, the instant on and off of LED-UV lighting eliminates the need for substantial standby power.
*In the case of the 920 model
Power consumption of the LED-UV curing system is only 10 percent* of that of conventional UV lamp system. In addition, the instant on and off of LED-UV lighting eliminates the need for substantial standby power.
*In the case of the 920 model
Long-life light source
A conventional UV lamp system’s light source lasts approximately 1,000 to 3,000 hours*, but the LED-UV curing system’s light source has a long life of approximately 15,000 hours. Moreover, a conventional UV lamp system remains lit in standby mode during makeready work, shortening its life, while the LED-UV curing system remains completely off so light source life is unaffected.
* Life cycle of the UV lamp depends on such conditions as on and off frequency.
A conventional UV lamp system’s light source lasts approximately 1,000 to 3,000 hours*, but the LED-UV curing system’s light source has a long life of approximately 15,000 hours. Moreover, a conventional UV lamp system remains lit in standby mode during makeready work, shortening its life, while the LED-UV curing system remains completely off so light source life is unaffected.
* Life cycle of the UV lamp depends on such conditions as on and off frequency.
Ozone-less and low heat generation
The LED-UV operates within a UV wavelength where no ozone is generated, eliminating the ozone odor peculiar to UV printing.
The minimal heat generated during curing reduces thermal impact on the printed sheets and eliminates the need for exhaust ducting.
The LED-UV operates within a UV wavelength where no ozone is generated, eliminating the ozone odor peculiar to UV printing.
The minimal heat generated during curing reduces thermal impact on the printed sheets and eliminates the need for exhaust ducting.
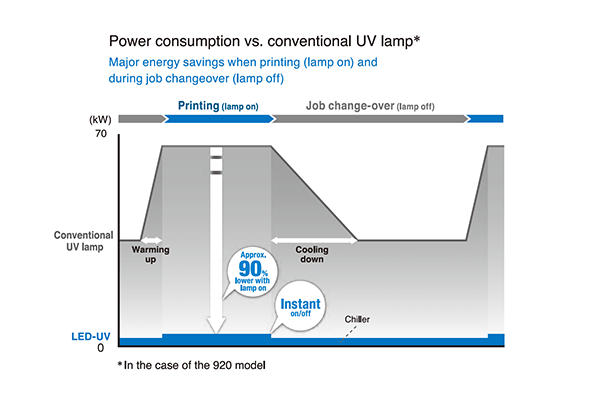
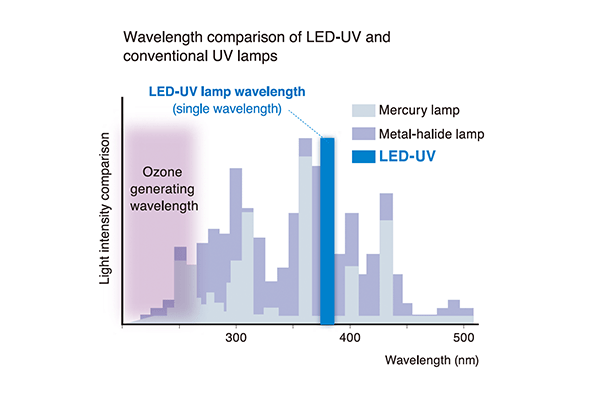
Varnish and special substrates for high-value-added printing*
The growing popularity of the LED-UV curing system has led to a wider selection of inks, varnishes and substrates. An array of high-value-added printing services can be offered by combining special colors such as gold and silver, various varnish coating surface treatments, and printing on special substrates.
* Drying performance may vary depending on printing conditions such as paper, ink , varnish, drying unit and printing speed and etc.
* Drying performance may vary depending on printing conditions such as paper, ink , varnish, drying unit and printing speed and etc.
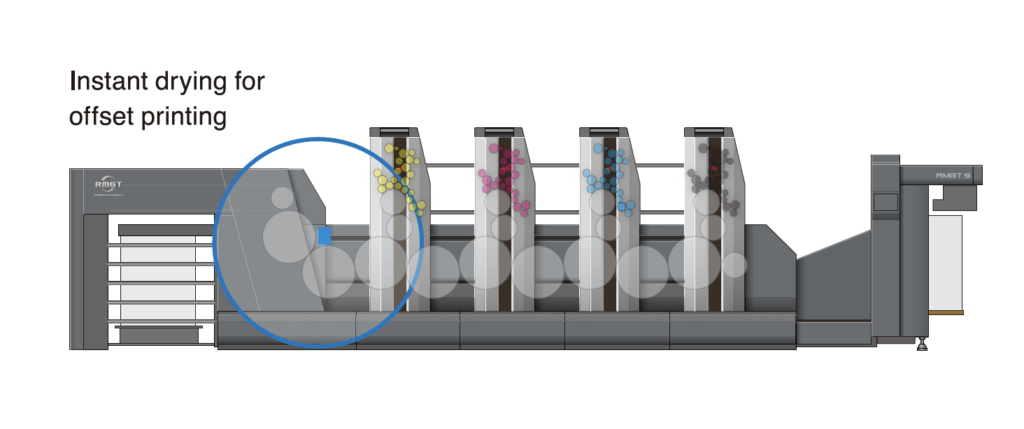
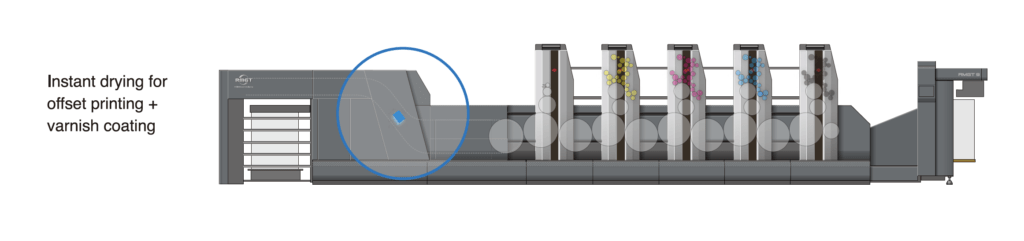